图书介绍
机械制造技术基础 第2版PDF|Epub|txt|kindle电子书版本网盘下载
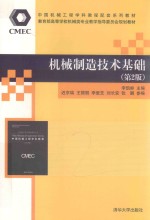
- 李凯岭,迟京瑞,王丽丽,李爱芝,刘长安,张鹏著 著
- 出版社: 北京:清华大学出版社
- ISBN:9787302489139
- 出版时间:2018
- 标注页数:429页
- 文件大小:61MB
- 文件页数:450页
- 主题词:机械制造工艺-高等学校-教材
PDF下载
下载说明
机械制造技术基础 第2版PDF格式电子书版下载
下载的文件为RAR压缩包。需要使用解压软件进行解压得到PDF格式图书。建议使用BT下载工具Free Download Manager进行下载,简称FDM(免费,没有广告,支持多平台)。本站资源全部打包为BT种子。所以需要使用专业的BT下载软件进行下载。如BitComet qBittorrent uTorrent等BT下载工具。迅雷目前由于本站不是热门资源。不推荐使用!后期资源热门了。安装了迅雷也可以迅雷进行下载!
(文件页数 要大于 标注页数,上中下等多册电子书除外)
注意:本站所有压缩包均有解压码: 点击下载压缩包解压工具
图书目录
第0章 绪论1
0.1 生产与制造1
0.1.1 生产的含义1
0.1.2 生产过程的定义与分类2
0.1.3 产品制造的含义3
0.1.4 制造技术3
0.1.5 工艺过程4
0.2 机械制造业在国民经济中的地位及其发展4
0.2.1 机械制造业在国民经济中的地位4
0.2.2 机械制造业的发展5
0.2.3 我国机械制造业面临的挑战和机遇7
0.3 “机械制造技术基础”课程的内容、特点和学习方法9
0.3.1 本课程的内容9
0.3.2 本课程的性质和学习要求10
0.3.3 本课程的特点及学习方法10
习题与思考题11
第1章 金属切削基础12
1.1 切削运动与切削用量12
1.1.1 切削时的工件表面12
1.1.2 切削运动14
1.1.3 切削用量14
1.2 金属切削刀具的几何参数15
1.2.1 刀具切削部分的结构要素16
1.2.2 确定刀具切削角度的参考平面16
1.2.3 刀具几何角度参考系17
1.2.4 刀具的标注角度18
1.2.5 刀具的工作角度20
1.3 切削层参数与切削方式23
1.3.1 切削层参数23
1.3.2 切削方式24
1.4 刀具材料及选用25
1.4.1 刀具材料应具备的性能25
1.4.2 刀具材料25
习题与思考题31
第2章 金属切削的基本规律及其应用32
2.1 金属切削过程中的变形32
2.1.1 挤压与切削32
2.1.2 切削层金属的变形33
2.1.3 刀-屑接触区的变形与摩擦36
2.1.4 切屑变形的规律38
2.2 切削力40
2.2.1 切削力的来源、切削合力、分力及切削功率40
2.2.2 切削力的求法41
2.2.3 影响切削力的主要因素43
2.3 切削热和切削温度45
2.3.1 切削热的来源及传出45
2.3.2 切削区的温度及其分布46
2.3.3 影响切削温度的主要因素47
2.4 刀具磨损与刀具寿命48
2.4.1 刀具磨损形态48
2.4.2 刀具磨损的主要原因50
2.4.3 刀具磨损过程及磨钝标准51
2.4.4 刀具寿命经验公式及其合理选择52
2.4.5 刀具破损55
2.5 刀具几何参数的选择56
2.5.1 前角及前刀面形式的选择57
2.5.2 后角的功用及选择60
2.5.3 主、副偏角的功用及选择62
2.5.4 刃倾角的功用及选择63
2.6 工件材料的切削加工性64
2.6.1 衡量切削加工性的指标65
2.6.2 影响材料加工性的因素66
2.6.3 改善切削加工性的途径66
2.6.4 难加工材料切削技术67
2.7 切削液的选择68
2.7.1 切削液的种类68
2.7.2 切削液的作用69
2.7.3 切削液的添加剂70
2.7.4 切削液的选择71
2.7.5 切削液的使用方法71
2.8 切削用量的选择72
2.8.1 选择切削用量的原则72
2.8.2 切削用量优化及切削数据库73
习题与思考题75
第3章 金属切削机床的基本知识76
3.1 金属切削机床的分类与型号编制76
3.1.1 金属切削机床的分类76
3.1.2 金属切削机床的型号编制方法77
3.2 机床的运动分析80
3.2.1 工件加工表面及其形成方法81
3.2.2 机床的运动83
3.2.3 机床的传动联系和传动原理图85
习题与思考题87
第4章 车床与车刀88
4.1 车床的用途、运动和布局88
4.2 CA6140型卧式车床的传动系统91
4.2.1 主运动传动链91
4.2.2 进给传动链94
4.3 CA6140型卧式车床的主要结构99
4.3.1 主轴箱内的主要结构99
4.3.2 溜板箱内的操纵机构104
4.4 车刀107
4.4.1 普通车刀的结构类型107
4.4.2 成形车刀的种类109
习题与思考题111
第5章 铣床、钻床、镗床及其刀具113
5.1 铣床和铣刀113
5.1.1 铣削与铣削方式113
5.1.2 铣床的主要类型116
5.1.3 铣刀119
5.2 钻床与孔加工刀具121
5.2.1 钻床的功用和主要类型121
5.2.2 麻花钻123
5.2.3 铰削与铰刀128
5.3 镗床与镗刀129
5.3.1 卧式镗床129
5.3.2 坐标镗床131
5.3.3 金刚镗床131
5.3.4 镗刀132
习题与思考题133
第6章 磨床与磨削134
6.1 磨削加工134
6.1.1 磨削加工概况134
6.1.2 磨削加工方法分类134
6.1.3 磨削加工技术的特点及应用136
6.2 砂轮137
6.2.1 磨料137
6.2.2 粒度137
6.2.3 结合剂139
6.2.4 硬度139
6.2.5 组织139
6.2.6 砂轮的形状140
6.2.7 超硬磨料砂轮简介141
6.3 磨削机理142
6.3.1 磨料的形状特征142
6.3.2 磨屑的形成过程142
6.3.3 磨削力的主要特征142
6.3.4 磨削温度143
6.3.5 砂轮的磨损及寿命144
6.4 常用磨床的类型及功用145
6.4.1 M1432A型万能外圆磨床145
6.4.2 平面磨床146
6.4.3 内圆磨床148
6.4.4 无心磨床(无心外圆磨床)149
6.5 表面的光整加工151
6.5.1 光整加工技术的功能及特点151
6.5.2 超精研151
6.5.3 研磨152
6.5.4 珩磨154
6.5.5 抛光154
6.6 砂带磨削155
6.6.1 砂带磨削机理155
6.6.2 砂带磨削的特点及应用范围156
习题与思考题156
第7章 其他机床与刀具158
7.1 齿轮加工机床与齿轮加工刀具158
7.1.1 插齿原理和插齿刀159
7.1.2 滚齿原理、齿轮滚刀及滚齿机的运动分析162
7.1.3 磨齿原理及所需运动168
7.1.4 锥齿轮的加工方法170
7.2 拉床和拉刀171
7.2.1 拉床的功用和类型171
7.2.2 拉刀172
7.3 刨床与插床175
7.3.1 刨床175
7.3.2 插床176
7.4 组合机床及刀具简介176
7.4.1 组合机床简介176
7.4.2 组合机床常用的刀具177
7.5 数控机床简介179
7.5.1 数控机床的概念与分类179
7.5.2 数控机床的特点180
7.5.3 JCS-018型立式镗铣加工中心181
7.5.4 自动化加工对刀具的要求182
习题与思考题183
第8章 机械加工工艺规程的制定184
8.1 机械加工工艺过程的基本概念184
8.1.1 机械加工工艺过程的组成184
8.1.2 生产纲领与生产类型186
8.1.3 机械加工工艺规程与工艺文件187
8.2 制定机械加工工艺规程的要求与步骤190
8.2.1 机械加工工艺规程的基本要求190
8.2.2 制定工艺规程所需要的原始资料191
8.2.3 制定加工工艺规程的步骤及主要内容191
8.3 零件加工工艺性分析与毛坯的选择191
8.3.1 分析零件技术要求及其合理性192
8.3.2 零件的结构工艺性审查192
8.3.3 毛坯的选择194
8.4 工件定位的基本原理195
8.4.1 基准的概念与分类195
8.4.2 六点定位原理195
8.4.3 六点定位原理的应用197
8.5 机械加工工艺规程设计中的主要定性问题198
8.5.1 定位基准的选择198
8.5.2 加工工艺路线的拟定200
8.5.3 机床与工艺装备的选择204
8.5.4 切削用量的确定205
8.6 加工余量及其确定方法206
8.6.1 加工余量的概念206
8.6.2 影响加工余量的因素206
8.6.3 确定余量的方法208
8.7 加工工艺尺寸的分析计算208
8.7.1 尺寸链的基本概念209
8.7.2 加工尺寸链概述212
8.7.3 加工工艺尺寸计算举例213
8.7.4 求解加工尺寸链的几种情况219
8.8 工艺方案的生产率及技术经济性分析220
8.8.1 生产率分析220
8.8.2 技术经济性分析221
8.9 提高机械加工生产率的工艺措施223
8.9.1 缩短单件时间定额223
8.9.2 采用先进工艺方法226
8.9.3 实行多台机床看管226
8.9.4 进行高效及自动化加工226
习题与思考题226
第9章 金属切削机床夹具设计230
9.1 机床夹具的基本概念230
9.1.1 机床夹具的分类230
9.1.2 机床夹具在机械加工中的作用231
9.1.3 夹具的组成231
9.2 定位方式与定位元件233
9.2.1 工件以平面定位及其定位元件233
9.2.2 工件以圆柱孔定位及其定位元件236
9.2.3 工件以外圆柱面定位及其定位元件240
9.2.4 组合表面定位242
9.3 定位误差的分析与计算245
9.3.1 定位误差的产生原因及组成245
9.3.2 定位误差的计算方法246
9.3.3 典型表面定位时的基准位移误差247
9.4 工件的夹紧251
9.4.1 夹紧装置的组成及基本要求251
9.4.2 夹紧力的确定252
9.4.3 典型夹紧机构255
9.5 典型机床夹具262
9.5.1 车床夹具262
9.5.2 钻床夹具265
9.5.3 镗床夹具271
9.5.4 铣床夹具277
9.6 数控加工典型夹具282
9.6.1 拼装夹具282
9.6.2 组合夹具284
9.6.3 多面高效数控专用夹具288
习题与思考题289
第10章 机械加工精度292
10.1 机械加工精度概述292
10.1.1 加工精度和加工误差292
10.1.2 经济加工精度293
10.1.3 获得加工精度的方法293
10.1.4 影响加工精度的因素295
10.1.5 原始误差与加工误差之间的关系295
10.1.6 研究加工精度的方法296
10.2 工艺系统的几何误差296
10.2.1 加工原理误差297
10.2.2 机床的几何误差297
10.2.3 工艺系统的其他几何误差301
10.3 工艺系统的受力变形302
10.3.1 工艺系统受力变形现象302
10.3.2 工艺系统的刚度303
10.3.3 工艺系统受力变形对加工精度的影响305
10.3.4 减少工艺系统受力变形的措施308
10.3.5 工件内应力对加工精度的影响310
10.4 工艺系统的热变形311
10.4.1 工艺系统的热源311
10.4.2 工艺系统的热变形对加工精度的影响312
10.4.3 减少工艺系统热变形的措施314
10.5 加工误差的统计分析315
10.5.1 加工误差的统计性质315
10.5.2 分布图分析法316
10.5.3 点图分析法321
10.6 提高和保证加工精度的途径327
10.6.1 直接减少误差法327
10.6.2 误差转移法328
10.6.3 误差补偿法328
10.6.4 误差分组法328
习题与思考题329
第11章 机械加工表面的质量331
11.1 机械加工表面质量的含义331
11.1.1 表面质量的含义331
11.1.2 机械加工表面质量对零件使用性能的影响333
11.1.3 表面的完整性334
11.2 已加工表面形成机理335
11.3 影响加工表面质量的因素335
11.3.1 影响表面粗糙度的因素335
11.3.2 影响加工表面层物理力学性能的因素338
11.4 机械加工过程中的振动342
11.4.1 受迫振动及其控制342
11.4.2 自激振动及其控制344
11.5 控制加工表面质量的途径348
习题与思考题350
第12章 非常规加工方法351
12.1 非常规加工方法概述351
12.2 电火花加工352
12.2.1 电火花加工的原理352
12.2.2 电火花加工的工艺特点和应用353
12.2.3 电火花线切割加工353
12.3 电解加工354
12.3.1 电解加工的原理354
12.3.2 电解加工的工艺特点355
12.3.3 电解加工的应用355
12.3.4 电解磨削355
12.4 激光加工356
12.4.1 激光加工的基本原理356
12.4.2 激光加工的工艺特点357
12.4.3 激光加工的应用357
12.5 电子束和离子束加工358
12.5.1 电子束加工358
12.5.2 离子束加工360
12.6 超声波加工361
12.6.1 超声波加工的基本原理361
12.6.2 超声波加工的特点361
12.6.3 超声波加工的应用362
12.7 快速成形技术362
12.7.1 概述362
12.7.2 光敏树脂快速成形363
12.7.3 层合快速成形365
12.7.4 熔融沉积快速成形367
习题与思考题368
第13章 机械装配工艺基础369
13.1 机械装配概述369
13.1.1 装配的概念369
13.1.2 装配工作的一般内容369
13.1.3 装配生产的组织形式370
13.1.4 装配精度的基本概念372
13.1.5 装配工艺性一般要求374
13.2 装配尺寸链及其概率解法375
13.2.1 装配尺寸链概述375
13.2.2 装配尺寸链的建立377
13.2.3 装配尺寸链的计算方法379
13.3 获得装配精度的方法380
13.3.1 互换装配法381
13.3.2 选择装配法381
13.3.3 修配装配法383
13.3.4 调整装配法386
13.4 装配工艺规程的制定390
13.4.1 制定装配工艺规程的基本原则及所需的原始资料390
13.4.2 制定装配工艺规程的步骤391
习题与思考题396
第14章 制造模式与制造技术的发展398
14.1 先进制造工艺技术398
14.1.1 超精密加工398
14.1.2 高速切削400
14.1.3 干切削403
14.1.4 成组技术404
14.1.5 计算机辅助工艺规程设计407
14.2 微机械和微机电系统制造技术的进展409
14.2.1 微硅零件的立体光刻腐蚀加工409
14.2.2 微器件的精密机械加工410
14.2.3 LIGA技术410
14.2.4 精微成形技术411
14.2.5 微型机械的装配411
14.3 机械制造自动化技术412
14.3.1 机械制造系统自动化412
14.3.2 柔性制造系统412
14.3.3 计算机/现代集成制造系统416
14.3.4 工业机器人417
14.4 先进制造生产模式419
14.4.1 敏捷制造419
14.4.2 并行工程419
14.4.3 JIT制造420
14.4.4 精良生产421
14.4.5 网络化制造422
14.4.6 虚拟制造系统423
14.4.7 可持续发展制造425
14.4.8 智能制造与智能工厂426
习题与思考题427
参考文献429