图书介绍
车削加工禁忌实例PDF|Epub|txt|kindle电子书版本网盘下载
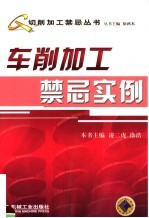
- 凌二虎,徐浩主编 著
- 出版社: 北京:机械工业出版社
- ISBN:7111160878
- 出版时间:2005
- 标注页数:451页
- 文件大小:14MB
- 文件页数:465页
- 主题词:车削-金属加工-禁忌
PDF下载
下载说明
车削加工禁忌实例PDF格式电子书版下载
下载的文件为RAR压缩包。需要使用解压软件进行解压得到PDF格式图书。建议使用BT下载工具Free Download Manager进行下载,简称FDM(免费,没有广告,支持多平台)。本站资源全部打包为BT种子。所以需要使用专业的BT下载软件进行下载。如BitComet qBittorrent uTorrent等BT下载工具。迅雷目前由于本站不是热门资源。不推荐使用!后期资源热门了。安装了迅雷也可以迅雷进行下载!
(文件页数 要大于 标注页数,上中下等多册电子书除外)
注意:本站所有压缩包均有解压码: 点击下载压缩包解压工具
图书目录
第1章 切削过程中的禁忌1
1.1 车削加工中不宜形成挤裂或单元切屑1
1.2 精车时不允许存在积屑瘤2
1.3 切削力不宜过大3
1.4 切削温度不宜过高6
1.5 不允许车刀出现过度磨损8
1.6 切削液的正确使用,不可忽视14
1.7 材料可切削性对车削生产率的重要影响,不可忽视18
1.8 化学元素对钢的可切削性影响,不可忽视19
1.9 钢的金相组织对可切削性的影响,不可忽视20
1.10 造成车削表面粗糙度值增加的两大因素,不可忽视20
2.2 各种刀具材料性能的差别,不可忽视23
2.1 刀具材料必须具备的性能,不可忽视23
第2章 车刀材料、车刀角度、车削用量选择的禁忌23
2.3 通用型、高性能高速钢性能与用途的差异,不可忽视25
2.4普通硬质合金、新型硬质合金和涂层硬质合金性能、用途的异同,不可忽视27
2.5 陶瓷车刀不宜在低速、冲击负荷下车削34
2.6 金刚石车刀不宜车削黑色金属工件,切削温度不宜过高35
2.7 立方氮化硼车刀不宜车削软材料及在低速、冲击载荷大的条件下切削36
2.8 选择车刀前角(γo)时,工件材料、刀具材料及加工条件的变化,不可忽视37
2.9 选择车刀前面形状及刃区参数时,工件、刀具材料性质及切削的特点,不可忽视39
2.10 切削塑性材料的断屑问题,不可忽视41
2.11 选择车刀后角(αo)时,工件材料及加工条件的变化,不可忽视43
2.12 选择车刀主偏角(kr)时,工艺系统的刚性及工件形状,不可忽视44
2.13 选择车刀副偏角(k?)时,工艺系统刚性及加工条件,不可忽视45
2.14 车刀切削刃上最薄弱部位形状的选择,不可忽视45
2.15 选择车刀刃倾角(λs)时,工件材料及加工条件,不可忽视46
2.16 车削用量三要素选择的顺序,不能颠倒48
2.17 选择背吃刀量αp时,余量大小与车削条件,不可忽视49
2.18 选择进给量f时,表面粗糙度要求与切削力的大小,不可忽视50
2.19 选择车削速度vc,刀具耐用度的保证与切削条件的变化,不可忽视55
第3章 车削工艺中的禁忌64
3.1 车床使用中的禁忌64
3.1.1 选择在车床上加工工件,不应背离车削加工的工艺特点64
3.1.2 车床传动系统图的重要作用,不可忽视71
3.1.3 识读车床传动系统图时两个关键问题,不可忽视73
3.1.4 车床精度及调整对加工质量的影响,不可忽视79
3.1.5 高精度工件车削、强力车削前,车床的调整,不可忽视94
3.1.6 车床的定期保养,不可忽视96
3.1.7 车床的维护保养,各部件的合理润滑,不可忽视97
3.1.8 操作车床,不得违反切削加工通用工艺守则99
3.1.9 操作车床,不得违反车削加工通用工艺守则101
3.1.10 操作车床,不允许违反安全操作规程103
3.2 车刀选用、刃磨、安装中的禁忌104
3.2.1 选用车刀,不可背离不同结构车刀的使用特点104
3.2.2 可转位刀片的厚度和精度,不可任意选择133
3.2.3 使用可转位车刀,不允许出现打刀等不正常现象135
3.2.4 夹紧可转位车刀刀片,要有防崩刃措施136
3.2.5 可转位车刀刀杆上刀片槽的两个定位面间的角度,不能大于或等于刀片的实际角度136
3.2.6 硬质合金可转位车刀刀片的法后角,不可任意选择136
3.2.7 刃磨车刀时,砂轮的选择不能有误137
3.2.8 手工刃磨车刀时,不能违背刃磨合理的顺序与安全操作138
3.2.9 车刀在刀架上的正确安装,不可忽视142
3.2.10 车刀安装位置对车刀前角、后角的影响,不可忽视144
3.2.11 车刀安装位置对车刀主、副偏角的影响,不可忽视146
3.2.12 进给运动对车刀工作角度的影响,不可忽视146
3.3 轴类零件车削的禁忌148
3.3.1 车端面时,刀具及进给方向的选择,不可忽视148
3.3.2 车削外圆表面,工艺与设备的选择,不可忽视150
3.3.3 在车床两顶尖间装夹工件车削外圆柱面时,两顶尖轴线不应错位151
3.3.4 中心孔类型的选择,不可忽视152
3.3.5 工件中心孔的加工质量,不可忽视155
3.3.6 在车床上钻中心孔,钻头折断的原因,不可忽视156
3.3.7 车削棒材毛坯的轴、盘、套类零件,棒材各157
部位加工余量,不可任意确定157
3.3.8 车削轴类零件,工序余量与车削步骤的选择,不可忽视163
3.3.9 切断刀的安装质量,不可忽视174
3.3.10 切断刀刀刃宽度及刀头长度,不可任意确定175
3.3.11 切断时,切断刀折断的问题不可不防175
3.3.12 影响车削质量的共同因素及改善途径,不可忽视177
3.3.13 轴类零件检测时,检测量具与检验方法不可有误201
3.4 盘套类零件车削的禁忌209
3.4.1 选择盘套类零件车削的工艺方法,其技术要求与结构特点,不可忽视209
3.4.2 盘套类零件孔加工的工序间余量,不可任意选择215
3.4.3 钻孔、扩孔、铰孔和镗孔的切削用量,不可任意选择221
3.4.4 刃磨麻花钻头常见的疵病,不可忽视234
3.4.5 车床上钻孔自动进给方式的应用,不可忽视235
3.4.6 钻孔时的操作调整,不可有误237
3.4.7 标准麻花钻结构的缺点及修磨方法,不可忽视238
3.4.9 同一直径尺寸的扩孔钻,其应用上的区别,不可忽视242
3.4.8 钻削不同材料的工件孔时,钻头的几何角度不应一成不变242
3.4.10 铰孔完毕时,铰刀退出工件的方式,不可忽视243
3.4.11 铰孔时,铰刀刀齿崩刃,不可忽视243
3.4.12 铰不连续孔铰刀结构的选择,不可忽视245
3.4.13 铰刀直径尺寸的极限偏差值,不可任意选择245
3.4.14 车内孔时,内孔车刀结构的选择,不可忽视248
3.4.15 车削盘套类零件,保证内、外圆位置精度的方法,不可忽视249
3.4.16 在三爪自定心卡盘上装夹工件进行粗车或精车时,其悬伸部分不宜过长256
3.4.17 三爪自定心卡盘上安装大直径工件时,不宜用正爪装夹256
3.4.18 用四爪单动卡盘装夹工件,校正工作,不可忽视257
3.4.19 钻孔时孔径扩大或偏小,不可忽视258
3.4.20 钻孔时孔的轴线歪斜,不可忽视260
3.4.21 钻孔时产生振动或孔不圆的现象,不可不防260
3.4.24 扩孔钻扩孔时,孔表面粗糙,不可忽视261
3.4.25 多刃铰刀铰孔时,孔径增大问题,不可忽视261
3.4.22 钻孔时孔壁表面粗糙问题,不可忽视261
3.4.23 扩孔钻扩孔时,孔径增大问题,不可忽视261
3.4.26 多刃铰刀铰孔时,孔径小的问题,不可忽视262
3.4.27 多刃铰刀铰孔时,不允许铰出的内孔不圆263
3.4.28 多刃铰刀铰孔时,不允许孔表面有明显的棱面263
3.4.29 多刃铰刀铰孔时,孔表面粗糙,不可忽视264
3.4.30 铰孔后不允许孔的轴线不直265
3.4.31 车削内孔时,孔的尺寸精度未达要求,不可忽视265
3.4.32 车削内孔时,不允许内孔的锥度超差267
3.4.33 车削内孔时,孔壁粗糙,不可忽视267
3.4.34 盘套类零件的精度检验,不可忽视267
3.4.35 车削轴、盘套类零件,提高生产率的途径,不可忽视274
3.4.36 提高钻孔生产率的途径,不可忽视278
3.4.37 提高铰孔质量与生产率的途径,不可忽视289
3.5 圆锥面车削的禁忌291
3.5.1 圆锥面加工方法的正确选择,不可忽视291
3.5.2 用转动小刀架法车削内、外圆锥面时,小刀架转动的角度不可不经换算296
3.5.3 车削配套圆锥面,不允许变动小刀架的角度298
3.5.4 车削对称圆锥孔,不允许变动小刀架的角度299
3.5.5 车削圆锥面时,不可不防废品的出现299
3.5.6 圆锥面精度的检验,不可忽视302
3.6 螺纹车削的禁忌306
3.6.1 螺纹车刀的安装方法不能有误306
3.6.2 车螺纹的三种进刀方式各具特点,不可混淆、误用307
3.6.3 选择螺纹车削方法,螺纹形状的特点,不可忽视311
3.6.4 车螺纹时扎刀、打刀不可不防311
3.6.5 车螺纹时不允许螺距超差312
3.6.6 车螺纹时,不允许螺距周期性误差超差313
3.6.7 车螺纹时,螺距积累误差超差,不可忽视313
3.6.8 螺纹车削时,螺纹牙形角不能超差314
3.6.9 车螺纹时,不能使螺纹中径几何形状超差314
3.6.10 车螺纹不应不防螺纹乱扣315
3.6.11 车削螺纹牙形,表面粗糙度值不允许超差315
3.6.12 机用丝锥攻螺纹时,丝锥崩刃、折断,不可忽视(一)316
3.6.13 机用丝锥攻螺纹时,丝锥崩刃、折断,不可忽视(二)319
3.6.14 机用丝锥攻螺纹时,丝锥崩刃、折断,不可忽视(三)320
3.6.15 攻锥螺纹的底孔尺寸与切削速度,不可任意选择322
3.6.16 使用特种丝锥,其结构特点和使用范围,不可忽视323
3.6.17 机用丝锥攻螺纹,不允许螺纹中径过大323
3.6.19 用板牙套螺纹时,毛坯准备、工具校正与切削速度的选择,不可忽视325
3.6.18 机用丝锥攻螺纹,不允许螺纹中径过小325
3.6.20 用螺纹切头切螺纹,梳刀崩齿问题,不可忽视326
3.6.21 用螺纹切头切螺纹,切头张开不灵、梳刀卡住工件不可不防327
3.6.22 用螺纹切头切螺纹,不能让螺纹乱扣328
3.6.23 用螺纹切头切螺纹,不允许螺纹中径椭圆328
3.6.24 用螺纹切头切螺纹,不允许螺纹中径超差328
3.6.25 用螺纹切头切螺纹,螺纹表面有波纹,不可忽视328
3.6.26 滚压螺纹的优点,不可忽视328
3.6.27 滚压螺纹的坯件材料硬度不能太高330
3.6.28 滚压螺纹前,坯件不能不倒角330
3.6.29 滚压头滚压螺纹时,滚轮张开量不足、工件退不出,不可忽视331
3.6.30 滚压头滚压螺纹,滚轮寿命低,不可忽视331
3.6.31 滚压头滚压螺纹,滚轮崩齿、碎裂不可不防331
3.6.32 滚压头滚压螺纹,不允许螺纹乱扣332
3.6.33 滚压头滚压螺纹,中径尺寸已小于下限,但过端环规仍通不过,不可忽视333
3.6.34 滚压头滚压螺纹,不允许出现螺纹不圆、三棱形或一边牙尖、一边牙平现象333
3.6.35 滚压头滚压螺纹,坯件不易进入滚压头,端部产生飞边或毛刺问题,不可忽视333
3.6.36 滚压头滚压螺纹,螺纹表面粗糙度值不应太大334
3.6.37 滚压头滚压螺纹时,不允许螺纹出现裂纹334
3.6.38 滚压头滚压螺纹时,不允许螺纹牙顶、牙侧产生毛刺、碎屑334
3.6.39 螺纹的检验,不可有误335
3.6.40 提高螺纹加工生产率的途径,不可忽视339
3.7 成形面车削的禁忌342
3.7.1 选择成形表面的车削方法,不应忽视工件结构、生产批量与加工要求342
3.7.2 用靠模法车削凸轮成形面,靠模表面圆弧半径不能任意选择350
3.7.3 顶尖式和卡盘式仿形车床加工型面的范围不能混淆351
3.7.4 仿形车削的型面与允许角度,不能任意选择353
3.7.5 仿形车削的工件型面与车刀工作主、副偏角,不能任意选择354
3.7.6 内仿形车削的型面与允许角度,不能任意选择355
3.7.7 内仿形车削的工件型面与车刀工作主、副偏角,不能任意选择356
3.7.8 仿形车削时,不允许外圆锥度超差357
3.7.9 仿形车削阶梯轴,较大直径的外圆尺寸扩大,以及内仿形车削阶梯孔,较大孔径的尺寸缩小,不可忽视357
3.7.10 仿形车削时,工件轴向尺寸忽长忽短,不可不防357
3.7.11 仿形车削时,倒角忽大忽小,不可忽视357
3.7.12 仿形车削时,圆弧半径扩大,不可忽视357
3.8 滚花、绕弹簧的禁忌358
3.8.1 表面滚花,滚花刀的选择和乱纹的防止不可忽视358
3.8.2 车床上绕制弹簧时,其心轴直径,不可忽视361
3.9 定位基准选择的禁忌363
3.9.1 工件车削时,定位粗基准的选择,不可忽视363
3.9.2 工件车削时,定位精基准的选择,不可忽视365
3.9.3 选择定位基准,不应使定位基准与测量基准不一致368
3.9.4 工件不能超定位368
3.10 车削零件结构的禁忌369
第4章 复杂、精密零件车削的禁忌376
4.1 车削细长轴,对其结构及工艺特点,不可忽视376
4.2 高速车削细长轴,不宜采用双支承跟刀架376
4.3 车削细长轴时不宜采用自右向左的进给方向377
4.4 车细长轴粗车刀主偏角不宜太小377
4.5 车削细长轴,工件弯曲问题,不可忽视378
4.6 用跟刀架车削细长轴时,出现竹节形误差不可不防380
4.7 车削细长轴,棱圆形(多边形)、麻花形误差不可不防381
4.8 车削细长轴时,出现锥度误差,不可忽视382
4.9 车削细长轴,工件出现腰鼓形误差,不可忽视382
4.10 车削细长轴时,表面粗糙度值大,不可忽视383
4.11 采用跟刀架车削细长轴,不允许存在超定位现象385
4.12 车削偏心零件,工件的结构、批量及加工要求的不同,不可忽视386
4.13 不同零件偏心距的测量方法,不可忽视392
4.14 大型薄壁件车削时,装夹变形问题,不可忽视394
4.15 环状薄壁件、薄片圆盘工件加工时,装夹变形问题,不可忽视395
4.16 微调刀头在精密孔加工中的应用,不可忽视396
4.17 金刚石铰刀加工精密孔的优越性,不可忽视397
4.18 深孔加工,其工艺上难点及相应的技术措施,不可忽视397
4.19 丝杠车削,其结构特点及保证质量的措施,不可忽视404
4.20 车削多头蜗杆,螺纹加工质量与分头误差的防止,不可忽视406
4.21 车削环面蜗杆,工件和刀具的安装不能偏离正确位置411
4.22 车削环面蜗杆齿形前,不可缺少蜗杆圆弧面的精车工序412
5.1 车削难加工材料,材料特性与切削特点的关系,不可忽视413
第5章 难加工材料车削的禁忌413
5.2 车削高强度钢、超高强度钢,刀具材料、几何角度与切削用量的选择,不可忽视414
5.3 车削高锰钢,其加工硬化严重、精度不易保证等特点,不可忽视416
5.4 用硬质合金群钻、可转位浅孔钻钻削高锰钢工件,防止崩刃和“闷车”,不可忽视419
5.5 车削淬硬钢、冷硬铸铁及耐磨合金铸铁,刀具磨损剧烈及崩刃问题,不可不防420
5.6 车削不锈钢、高温合金,保证加工质量的措施,不可忽视423
5.7 不锈钢、高温合金工件在钻孔时的断屑问题,不可忽视429
5.8 不锈钢、高温合金铰孔时,保证孔的质量,不可忽视432
5.9 车削工程塑料,材料回弹性等对加工质量的影响,不可忽视435
5.10 钻削热塑性塑料、热固性塑料钻头的材料与几何参数的区别,不可忽视438
附录441
附录一 切削加工用硬质合金的应用范围分类和用途分组441
附录二 三针测量螺纹中径时的M值443
参考文献451